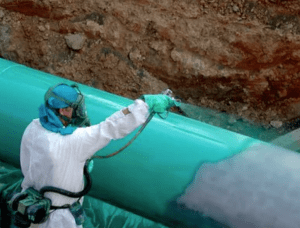
About Corrosion Protection
Why It Is Important
Exterior corrosion protection on tubulars in the industry is a vast and interesting science. Depending on service of the piping, its environment, and the expected design life, we can offer many solutions from a survey of pipeline integrity to detailed coating specifications, job bidding recommendations, contractors, and inspection of the installed systems.
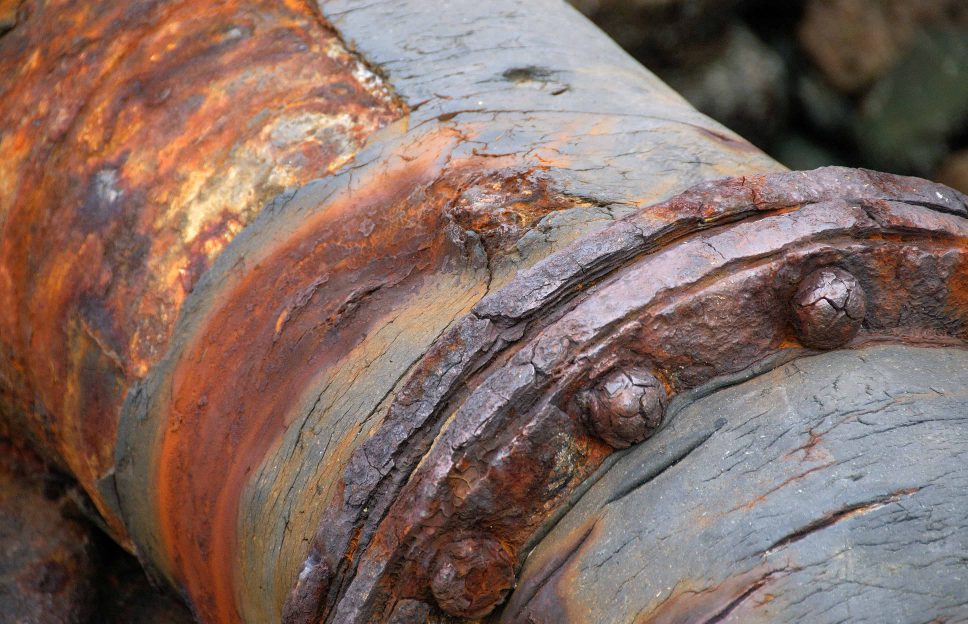
They are a firmly placed tool in the corrosion protection arsenal. These systems have been the traditional first line against corrosion over many years on pipelines and infrastructure. Their formulation technologies have varied, but their processes of application always require strict quality controls to remain effective and durable. It is absolutely necessary to have expertise in the selection of the right coatings to fit the task at hand. Vendor reliance for proper recommendation should be supplemented with oversight by a trained independent coatings industry professional and third-party inspection during application
Proper procedures and applications are critical in this environment as well as competent third-party inspection to ensure quality. The cost of application failure in this type of scenario is enormous.
Their ease of application and low surface preparation requirements make them an easy and reliable solution for long term corrosion protection. They are presently capable of effectively protecting pipe in much higher operating temperatures
On atmospheric installations, it has been a proven technology if applied properly and to correct minimum thicknesses.